Strong Arms Keep Lines in the Air
(see bottom of the article for a full Crossarm video)
The heavy line hanging from the arm of the derrick digger tightened and strained, pulling the 55-foot utility pole out of the roadside
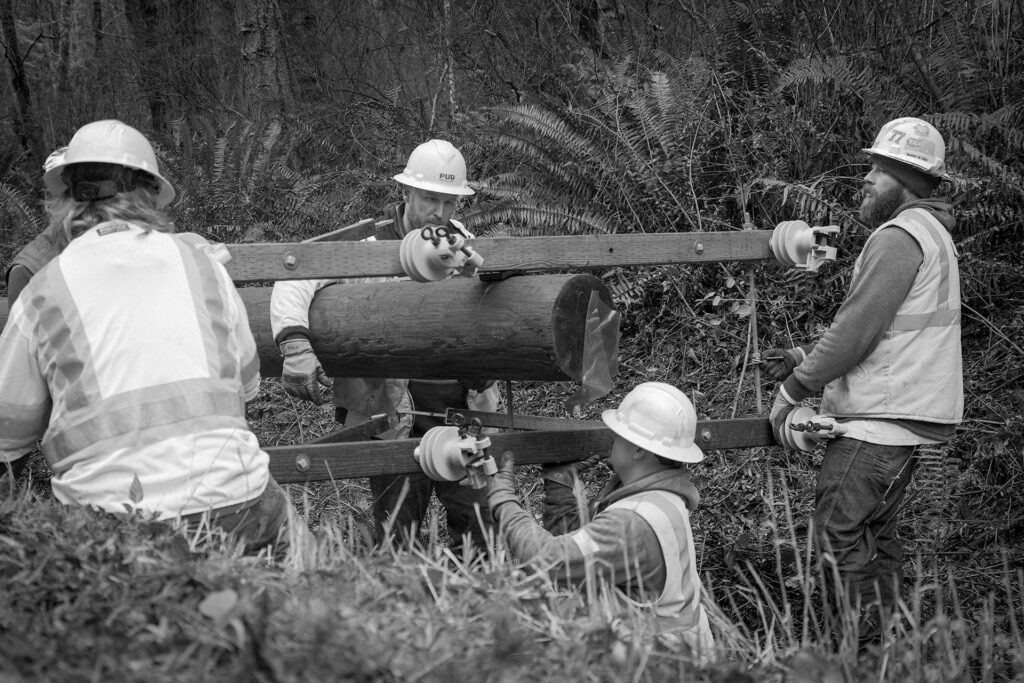
ditch. Line crew descended upon it and in minutes had fastened a dual crossarm assembly to the pole.
A crossarm is the horizontal component mounted toward the top of a utility pole that supports the power lines a safe distance apart and provides a connection point for insulators.
Moments later the 1,000-pound pole was hoisted skyward and positioned in its new home. The ease of replacement, even under less-than-ideal conditions, is all by design. Components, such as utility crossarms by regional supplier, Brooks Manufacturing, make the work faster and easier.
Locally Made – Nationally Known
Bellingham-based Brooks Manufacturing produces a large percentage of wooden utility crossarms nationwide, including most crossarms used by Jefferson PUD. Brooks’ 14-acre plant has been in operation since 1915 and is a blend of new age tech and tried and true old-world manufacturing.
Anywhere power goes in the U.S., there is a crossarm nearby designed to handle any weather Mother Nature doles out. The vast majority of crossarms in service are coastal Douglas fir harvested right here in the Washington, Oregon, Idaho, and British Columbia region. Coastal fir is the material of choice due to its rot-resistant nature, fire-resistance, and because pesky boring insects tend to stay away.
How it’s Made – Crossarm Production
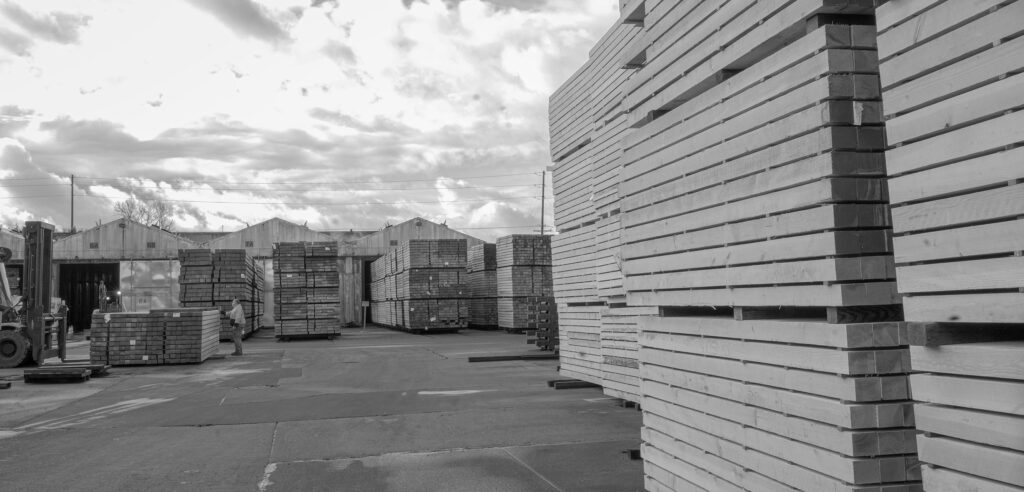
To maximize working lifespan (and meet National Electric Safety Code guidelines) lumber goes through a unique process before it hits the field.
Rough milled lumber arrives by the truckload and is stickered, which allows air flow between pieces for the drying process. Brooks has four steam-powered kilns designed to gradually pull moisture from the wood. Time in the kiln depends on the material size and can vary from 1 to 2 weeks at a consistent 180 degrees. The drying process is carefully monitored—drying too rapidly can cause twists, warping, and splintering.
Heat is a biproduct of steam pumped through piping from the 1950’s-era steam boiler which is 100% fueled by a combination of chips, off cuts, and saw dust produced during the milling process.
The rough-cut, dried lumber is then sent single file through a massive four-sided planer. In the matter of seconds material on all four
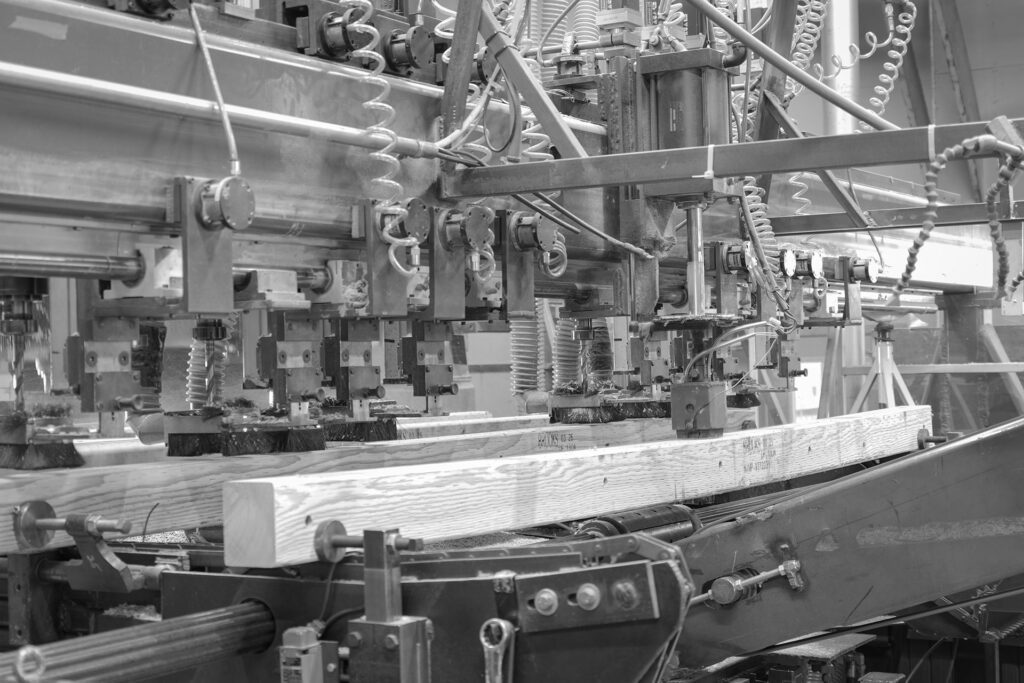
sides and the corners are rounded over. Indents are also placed on all surfaces to help with pressure treating.
The smooth crossarms then pass through a cut-off saw for final sizing. Crossarms are graded and sorted as they make their way from conveyor to conveyor to the automated boring process.
Bore placement on the newly minted crossarms is essential for safely connecting support braces, insulators, or brackets. Large drill bits accurately chew through the material from the top and sides, and each crossarm receives a brand indicating the manufacturer, material type, and top for line crew.
The final step is pressure treating. Though naturally rot-resistant, pressure treating crossarms helps extend the usable life further, lasting up to 60 years under ideal conditions.
Crossarms are loaded into a submarine-shaped chamber which is flooded with treatment solution and pressurized up to 100psi–the equivalent of diving approx 200 feet underwater. Pressure forces air trapped inside the wood outward, replacing it with the preservative. A vacuum is then applied to pull excess solution and moisture from the wood. Total time in the chamber is approx 4 hours.
The crossarms are removed and placed under cover until they are ready to be loaded up and put into service.