What’s that? Overhead vs Underground Lines
Each year, the PUD makes strides toward the undergrounding of distribution lines countywide. In this ‘What’s that?’ we will compare distribution lines, the cost to place them, and how the PUD plans for a subterranean future.
First, let’s look at the contenders.
Overhead Line: In the above ground corner, weighing in at approximately one-quarter-pound-per-foot we have #2 ACSR. Aluminum Conductor Steel Reinforced (ASCR) is one of the most common distribution lines used in our county. JPUD currently has 373 miles of aboveground distribution lines across the county. There’s a lot packed into this seemingly simple cable starting with the strands of aluminum conductor spiraled around steel reinforcement. Steel has a much stronger tensile strength (resistance to breaking) than aluminum, but aluminum is more conductive than steel–meaning electricity flows through aluminum a bit better. Steel reinforcement is needed because of the forces at play above ground.
While below ground utility lines can lazily sit comfy and cozy in their conduit, above ground they must withstand all of Mother Natures fury and the inevitable tug of gravity. Utility poles are often spaced 200′-300′ apart, which means each line can weigh up to several hundred pounds between poles. Add to this the infrequent ice storm which can coat lines with an inch or more of ice, and you can see where the steel reinforcement really helps.
There’s a lot of pressure on above ground lines, as entire sections of utility poles are engineered to support and distribute the weight. Utility lines are tensioned to ensure they do not sag close to the neutral (located below the primary lines), and to avoid contacting each other during high wind events.
Underground Line: Below ground, buried under 42″ of dirt and nestled within conduit (sometimes), is specialized distribution cable. Out of sight, out of mind…until an outage occurs. The majority of underground line in Jefferson County is direct-bury, meaning it does not have a protective conduit which increases the potential for an outage. All new construction in Jefferson County requires in-ground construction with conduit per PUD engineering standards.
For the vast majority of direct-bury lines, being 42″ or more underground is a safe place to be–moles and other subterranean critters typically burrow 36″ or less and are unlikely to square off with a utility line. Most commonly, trouble lies with the unlikely, infrequent visitor from above: us. Digging or boring operations are a common (and avoidable!) cause of underground outages. By calling the free 8-1-1 Call Before You Dig service you automatically put the word out to all water, sewer, power, and telecom companies who may be impacted by the work you intend to do. Companies have 48 hours to respond, and their response will be visible by colored coded paint on the ground indicating where underground utilities are located. If there’s paint in your planned work space, find a new spot to dig–but call 8-1-1 for the new site as well!
Besides people, normal environmental factors such as sharp rocks or tree roots can also impact underground line. Additionally, the age of the line is also a factor. Buried line often has a 20 – 30 year lifespan.
But isn’t the buried line like the overhead line? Reinforced aluminum and steel?
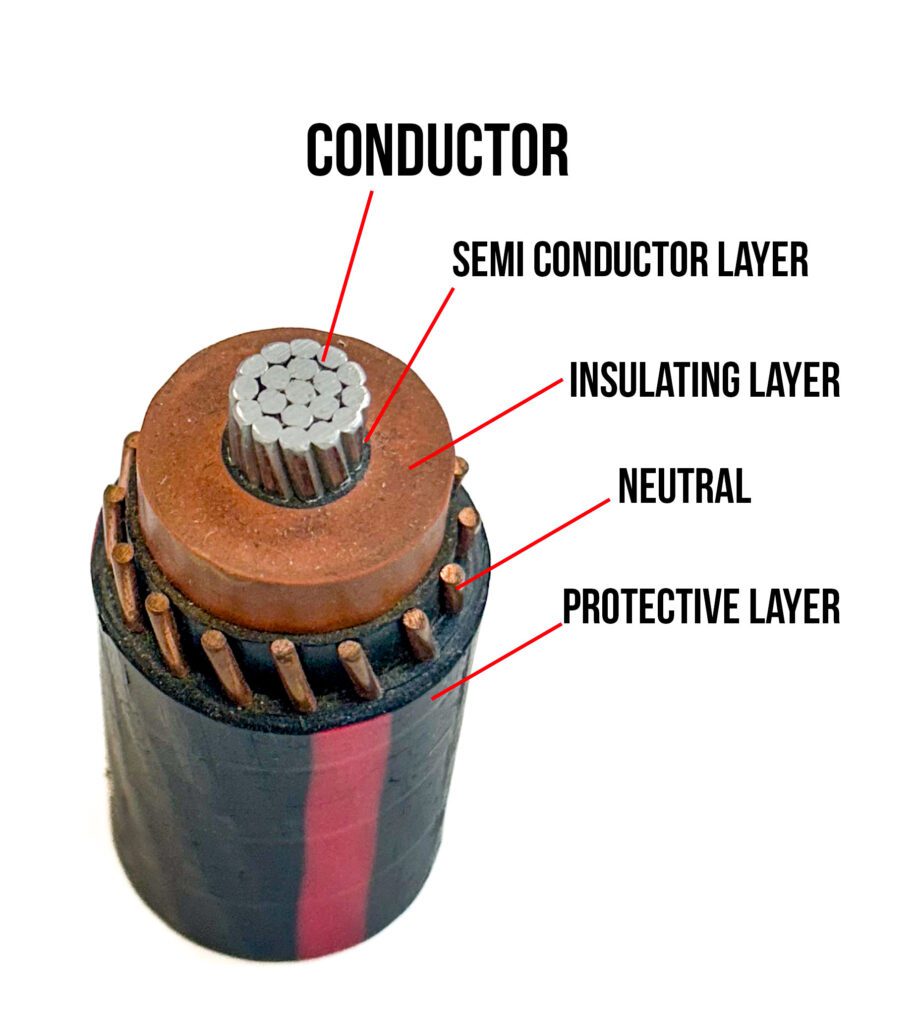
Yes and no.
The bread & butter underground distribution line in use today is insulated 1/0 cable. This line features a unique cross section resembling a cutaway of the earths core. In the center is the conductor itself (steel/aluminum) and a thin semiconducting wrap separating it from the next layer. Encasing the conductor is a thick insulating layer called EPR rubber, which is similar in feel to a heavy duty pencil eraser. The next layer is an evenly-spiraled mix of copper within the molded protective coating. The resulting line is impressive and quite strong, but also has an achilles heal.
If the protective outer coating is punctured the energy traveling within can escape and seek a path to ground, causing an outage.
In most cases these punctures (commonly caused by rocks pressed into the power line by years of earthen pressure or tree root growth) is no larger than a pin-prick. That tiny, nearly imperceivable hole allows a river of energy to flow, much like a crack in a dam growing larger and larger from water pressure. Except the flow of energy is often instantaneous, leading to an outage.
To locate the outage, crews connect a detection device which delivers a large shot of energy to the damaged line. The pin-prick-sized issue suddenly grows, and crew members above ground can hear the fault occurring and know where to dig for the repair. A dirt work contractor is called in and the affected areas is exposed and repaired. This is an expensive and time consuming process.
Conduit for underground line is not a guarantee to stop faults, but it certainly can help. Microscopic defects in the insulated line can absorb water and cause a fault. In the case of conduit, crews can simply disconnect the section of line between the in-ground vaults and pull it free to make repairs/replace the section. This greatly improves repair times by not having to dig for each outage.
Pros and Cons
Clearly, each line type has its pros and cons, but what about cost?
- Underground line is often 2 – 5x more expensive for the cable itself than overhead line.
- Underground distribution line requires 3″ conduit.
- Undergrounding can be done via an open trench or conduit can be pulled through with a boring machine. Boring can cost up to 5x more than open-trench construction.
- Overhead lines require far less time to repair–most repairs require a simple in-line splice if a section is damaged.
- Overhead lines require constant utility pole and exposed equipment upkeep.
- Overhead lines are exposed to natural (landslides, lightning, trees, etc) and man-made hazards (car vs pole).
- Underground line requires a dirt work contractor on-call to access damaged area.
Clearly, installing and repairing overhead line is financially beneficial, however, JPUD has set a primary focus on reliability (keeping our customers energized by minimizing outages) and safety, and undergrounding of lines is an additional focus for the longevity of our grid.
As part of the PUD annual capital projects workload, our engineering and operations staff look at historic outage data to locate sections of distribution line to pinpoint likely overhead-to-underground conversions are needed most.